From Bonfires to Kilns
After Man had learned to make a fire, it didn't take long before he discovered that anything made of clay became permanently hard after being in a hot bonfire for some time. In the last two tutorials this has already been referred to.
Communities all over the world learned to make pots and fire them in bonfires. The methods used were very similar.
More preparation and more brushwood was necessary if a lot of pots were to be dried and fired. But it was a more efficient method than firing pots singly and losses through cracking and exploding were fewer.
Firing many pots together was also a periodic communal event, needing a team spirit to keep the fire going the whole day.
Where pottery making became an organised craft, the bonfire site was often excavated to a shallow pit and covered with a good layer of brushwood on top of the charcoal and ashes of the previous firing. Then the sun-dried pots would be stacked on top, usually upside down, and depending on the size, layer upon layer. Over the top layer of pots a covering layer of broken pieces of fired pots from previous firings was carefully laid. This protected the pots from cold winds during and after the firing which reduced the risk of cracking. Finally more brushwood on top and the bonfire was ready to light.
The Updraft Kiln
The change from bonfire to a furnace or kiln was in order to get better control of the fire. Heated air rises; this principle governed the way kilns evolved. The invention of the simple updraft kiln can only be deduced from a few ancient illustrations, mostly Early Egyptian. Maybe the idea evolved independently in different parts of the world. It is quite possible that a kiln or furnace was developed first to smelt copper ores with charcoal in order to produce copper metal. All early communities which were well organised probably tried various ways to improve their firing methods. Probably the pottery kiln began with the circular containing wall for the bonfire pit. Built out of lumps of local stone and pottery shards from previous firings, it was mortared together with plenty of clay mud. A number of openings were often made to use as stoke holes. These could also be used to collect the fired pots afterwards.
In the more sophisticated version shown here, we can see that the protective covering of pottery shards has been replaced by a domed roof with holes left in to allow heat and smoke to escape. This dome was made of pieces of broken pots, clay mud and straw or chopped grass. It was built(or spread) over the pile of unfired pots. After the firing, it would have been broken open, and completely or partially removed as shown here. The advantage of the dome was a better draft of air sucked up through the stoke holes, up through the pots and out through the dome. This was much more efficient than a bonfire, the firings were more even and there were fewer losses.
Updraft Kilns in Egypt
No examples of Egyptian kilns have been found but the simple updraft seems to have been used here. These two drawings from tomb wall paintings seem to show tall domes kilns. On the left the potter seems to be lighting the fire at the base. On the right a potter seems to be climbing up to the top of the kiln and either plastering down the roof or perhaps lifting out fired pots. The near nakedness of the two potters on the right side of the larger image tells us how hot the atmosphere was around these simple kilns.
Updraft Kilns in Crete
Throughout the Middle East and the Mediterranean this pattern of kiln building was copied and developed further. The size, actual shape and materials varying widely. This one was actually in use in a Cretan village within the last decades of the 20th century. It is a traditional shape and structure which has been handed down for countless generations. When I saw it in use the fuel was mostly a vast amount of vine prunings! Most of the kiln is built out of rough lumps of stone and pottery shards with clay mud. This kiln did not have a plastered dome covering, instead just a large amount of broken fired pots laid on top of the mass of unfired pottery beneath.
The most important improvement or innovation here was the separation between a firebox at ground level and a supported but perforated shelf above which formed the base of a separate kiln chamber for the pottery. This floor was constructed in fired bricks or pieces of stone and arranged in an open chequered pattern or drilled holes to allow the heat and flames to pass upwards into the chamber and through the stacks of pots. From writing and tomb paintings we know that this type of updraft kiln was being used in Egypt, Mesopotamia and Crete during the second and first millennium BC.
Updraft Kilns in Greece
Drawings on Greek pottery show us some of the further improvements made to kilns used in Greek cities, and probably elsewhere, during the last half of the first millennium BC.
The main difference is that the beehive-like kiln shape is permanent and enclosed. There is a door opening which can be bricked up for firing. It allows the pots to be loaded in and later removed quite easily.
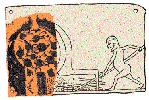 A worn pottery fragment showing a loaded kiln from ancient Greece - with an added line drawing reconstruction. It is a stylised side view and a plan in one showing a kiln loaded with typical decorated jugs.
By the 5th Century BC., potters had achieved a considerable control over their firings through the development of these enclosed updraft kilns:
- Pots separated from the fire,
- A permanent chamber with a door or bricked up opening,
- a short chimney with provision for controlling the draft on atmosphere of the kiln using a tile,
- or by blocking or reducing firemouth opening.
Firing Pottery in the Roman World
From Western Asia to the Mediterranean the kiln designs and firing practices became very similar. By Roman times these techniques had spread to much of Europe. Brick and tile making became very widespread over the Roman Empire. Kilns themselves were now often made of fired bricks. The firing temperatures would typically be from 800° - 950°C. and mostly red earthenware often decorated with red, brown, cream or white slips. Only as we approach the end of the millennium to we see much evidence of poured or brushed glazes on pots, but this does not become widespread for many centuries still in the Western world. - Read the the next tutorial.
Other important types of kilns, such as Oriental kilns, which evolved separately, or much later, are the subjects of later tutorials.
Summary: Tutorial No.3. Early firings
- The earliest potterty ca. 7000 BC. was fired in bonfires.
- Probably before 2000 BC. the principle of the updraft kiln was being explored.
- The principle that warm air rises guided the building of kilns.
- From the second to the first millenium BC. the updraft kiln was developed and refined in Western Asia and the Eastern Mediterranean region.
- All pottery made at this time was fired from 750° - 900°C., was unglazed and only decorated with red, white or black slip. Usually pots were piled on top of each other.
- From perhaps around 1500 BC. there were attempts to apply a soda frit glaze on bricks and pots. Probably different types and sizes of kilns were built for tiles, pots and frit paste. The Cretan potters, and the Greeks later on, refined the control of the atmosphere in their kilns using simple but effective methods.
- By the time of Christ pottery-making was a large scale affair in the Roman World, the kilns were all of an updraft type, based on the examples illustrated.
|