|
Dating Problems
Charting this early story is difficult. Archaeological dating from 3000 BC down to about 1000 BC is often confusing, contradictory and still not reliable. Nevertheless, in these early tutorials I have tried to present the broad sweep and sequence of events with dates that, as far as is possible, come from authorities I respect.
But A Real Glaze Took Much Longer
Potters in those early civilisations had made a self-glazing blue material, but had no concept of an applied glaze or how to make one. It took many centuries, even millenia, of trial and error soda frit paste mixtures and firings, before the principles of glaze making were even superficially understood. The production of a practical ceramic glaze recipe, which could be mixed and poured or brushed onto a clay pot, took probably another two thousand years from the making of the first frit paste.
Examples of Blue Quartz frit Paste
The tiny press moulded beads illustrated here are made of quartz frit paste. They were found in Egyptian tombs and date from at least 1500 BC
This little figurine is about two inches high. It was press moulded, decorated with black pigment(iron/cobalt/manganese minerals), allowed to dry and then heated in a kiln to about 850°C. Countless thousands of these figurines were made and placed in a dead person's tomb. It was believed that they became substitutes - "ushabtis" - for the dead person's spirit and could perform unpleasant or manual tasks on his behalf during his journey through the underworld. Often boxloads were place in a tomb. This explains why they are amongst the most common pieces of blue frit ware found.
This little dish is about six inches diam. made in the early 18th Dynasty. c.1450 BC. It was press moulded, painted with a dark slip and allowed to dry. As the moisture evaporated a powdery white covering of soda covered the design. When fired, the heat of the kiln caused the soda concentrated on the surface to melt the fine quartz and form a glaze. The bright turquoise glaze was produced by just the small amount of copper compound mixed with the quartz sand and soda which, with a tiny amount of water, formed the frit paste mixture. The dark slip design becomes black under the soda glaze after firing.
The Egyptians made a variety of small objects in quartz frit paste. Modelled figures like this one of the hippopotamus goddess, the protectress of the pregnant wife, are good examples of how refined the technique became in the New Kingdom(or Empire) period when Egypt had become rich and powerful. Notice the painted lotus flowers growing in the swamps through which the animal foraged along the edges of the river Nile. Made about 1400 BC, the brush drawing was done in a dark slip containing manganese and iron compounds.
The Most Innovative Makers of frit Paste
During the first half of the second millennium Cretan craftsmen were probably the most inventive designers in frit paste. Many were employed in Egypt where they influenced much sophisticated Egyptian work in the latter half of the second millennium BC Unfortunately pieces of Cretan style frit paste not found in the dry warm tombs of Egypt are usually like this one in poor condition. In Crete, damp and cold has worn or rotted away much of the shine and bright colour. This flat back panel of a goat suckling her young is lively and naturalistic but it has lost most of its rich blue, white and green colours. In spite of their poor condition, the small press moulded figure panels and the small figurines show us how inventive Cretan artists were. The panel was found in the temple repositories at Knossos along with the figurine of the snake goddess. Made c.1500 BC
Cretan style frit paste drinking vessel called a rhyton. Made about 1400 BC, it was found in an Egyptian tomb. The presence of this typical Aegean ceramic shape in Egypt underlines the influence of Cretan craftsmanship and the internationalism of so much design in the eastern Mediterranean region during much of the second millenium BC
"Egyptian" Blue or Kyanos
A broken piece of quartz frit paste; it is only the outside which is glassy and blue. The inside of the body is hard and granular, speckled and greyish.
This blue powdered material is considered a variation of blue quartz frit paste. Often called "Egyptian Blue", in the classical world it was known as "kyanos" - an ancient Greek-Mycenaean-Minoan term meaning dark blue enamel. Although archaeological experts seem not to be sure of its exact composition, most experienced potters would readily accept that it was developed from quartz frit paste. See my tutorial on Cretan & Mycenaean Ceramics for more information.
Manufacture: Pieces of fired blue frit would be crushed into a greyish powder, mixed with more soda and some lime, then refired. Crushed again, the powder would now have become a chalky blue colour throughout. Variation in the amounts of soda and lime added, and different degrees of heat in the firing would result in a paler or darker chalky blue throughout the body. There would be little if any shine or glaze outside. The process could be repeated to get a particular intensity of chalky blue, then crushed into a fine powder and made into a paste. It would be used for press moulding, dried and fired to make hard and permanent. It would become a hard fine-grained material like a blue mineral which could then be carved, drilled and polished. It was often combined and contrasted with quartz frit when used for making small objects or jewelry. Another use was as a permanent blue pigment for wall painting. Do email me if you want recipes to test.
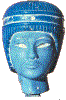 This beautiful head of Queen Nephertiti was made in the Amarna Period, about 1560 BC The Hair or Wig was press moulded in dark blue quartz frit paste and the face, head and neck made separately from smooth fine-grained pale blue Kyanos. The head was probably press moulded first and refined by carving and drilling then finally polished. Precious stones may have been added in the headdress.
An Egyptian press moulded bowl in a pale chalky blue kyanos. Notice crisp and detailed press moulded patterns and the soft shine of the surface, unglazed but smooth. It was made in the 18th dynasty.
This two inch fragment of a winged figure comes from Assyria - press moulded in kyanos(Egyptian Blue). Pieces like this confirm that this material and the making techniques had spread throughout the Middle Eastern world by the 14-13th centuries BC
Frits of Many Colours - The Cretan Legacy
By the 16th century BC the Cretans had developed the range of other colours that can be obtained by adding small amounts of different metal compounds.
This little frit paste figurine was made in the 15th century BC in Minoan Crete. It has been known as the Snake Goddess since it came to light in the 19th century when the site at Knossos, described as the treasury of the sanctuary, was being excavated. It was built up from pieces of differently coloured frit paste for arms, head, costume, etc. which were then stuck together. After more than 3000 years in cold damp soil, it is rather worn, much of the original bright colour has gone, but is nevertheless evidence of the superiority of the Minoan craftsmanship. During the century that followed, their craftsmen introduced the Egyptians and the people in the coastal cities of Western Asia to these new colours. Egyptian wall paintings show Cretan craftsmen at work in Egypt. Jewelry, tomb furniture and ceramics show the strong Minoan influence during the Egyptian New Kingdom - from Amenophis IV to Tutankhamen and later still.
This Egyptian frit paste figurine is in a near perfect state compared with the previous multicoloured figurine from Crete. That is a testimony to the dry steady atmosphere of the tomb in which it was found; Medinet Habu at Luxor. Made about 1200 BC The technique is the same as the Cretan figurine; a composite piece made from press moulded shapes of brown, black and white coloured frit paste. By comparison with the Cretan figurine, this Egyptian figurine is much less refined and sophisticated than the earlier piece from Knossos.
These two little inlaid pieces of frit paste are just over an inch wide (3.2cm) They are from a group of over a dozen found with other important pieces, such as the frit paste Snake Goddess figurine, on the Knossos site in Crete. They were made c.1550 BC at least two hundred years before objects like the necklace we examine next which was found at Amarna in Egypt (the time of Amenophis IV, Tutankhamen and Nephertiti). where the same techniques reappear. As I've remarked before, the state of all these Cretan pieces is poor and worn but though lacking in colour, they illustrate the delicate inlay technique of tiny strips of different coloured frit paste inlaid into a base shape. These tiny plaques represent the facades and structure of Cretan houses, which is confirmed by comparison with Minoan houses excavated on the island of Thera to the north of Crete. Colours include pale blue, green, red, white and black. What these pieces were for we can only guess, - loom weights, inlay for furniture. These are just guesses. From all these objects there is clear evidence for a highly independent quartz frit paste industry in Crete c. 1750 -1450 BC Middle Minoan III. This is at least two hundred years before such a high standard of work appears in Egypt (Amarna Period)
The Amarna period (1372-1362BC)was the peak of Egyptian decorative design and this fritware polychrome necklace shows that the advances in making techniques and colour technology had reached Egypt by the 14th century BC, in the 18th dynasty of the New Kingdom. This piece was almost certainly inspired, and probably made, by some of the many Cretan craftsmen working in Egypt at this time.
This detail of the necklace shows something of the quality and the technique. Bold bright yellows, greens, pinks, purples and reds were now available. The bottom row shows the blending of different pieces of coloured frit paste. The triangular end piece is made of a neutral coloured piece of frit paste. Tiny elongated arrow shaped strips of paste in copper blue, cobalt blue and manganese purple have been pressed into the pale body. The piece was allowed to dry so that there would be a soda build-up on the surface to give the shiny glaze. After firing, the tiny shapes became softened and melted slightly together at the edges. This detail allows you to see the subtle effect of this softening. It imitates the form of the lotus flower.
Tiles And Panels Made of Inlaid frit Paste
Still in Egypt but moving on 300 years, towards the end of the second millennium. Decorative frit panels in the Palace of the Pharaoh Ramesses III (1187-1156 BC) at Medinet Habu, Thebes. This Pharaoh was the last great king of the New Kingdom. Here we can see how the inlay technique used in the small Cretan plaques and in the lotus flower of the necklace could be used for large figure panels to decorate the door and walls of a palace.
. Made about 1150 BC these five panels of coloured quartz frit paste are richly inlaid with different colour shapes to represent a range of ethnic types in different national costumes. They represent the neighbours, traders, enemies or slaves of imperial Egypt. The walls of the palace were originally covered with such panels which must have given an impression of great brilliance. By now they were using a range of other minerals besides copper ore to produce a wide spectrum of coloured pastes. On panels such as this the inlaid strips and pieces could be pressed, modelled or further inlaid to create subtle textures or particular effects.
This detail of the head and shoulders of this dark skinned Nubian also shows part of the costume. This inlaying technique enabled the artist to create subtleties of form, pattern and texture of fabric and also depict a distinct racial type. The making of national costumes in these panels is very impressive. The whole process would not have been easy. The difficult medium, such a variety of tiny pieces of coloured paste to be cut, pressed and stamped and carefully dried and the firing process would have been tricky.
frit paste into Glaze?
As one moves down through the second millennium the inlays of coloured fritpaste become increasingly intricate and with careful firing, which caused greater softening of the inlay, some pieces of fritware had a more smooth and even surface. We could easily mistake some of these for thick slip brush decoration under a glaze. To the ancient potters this development must have been considered a considerable refinement.
This is the remaining top section of a fritware rhyton - a conical shaped Cretan type drinking vessel. It was found at Kition in Cyprus and is dated to the 13th century BC The yellow and red frit glazes are contained between lines or furrows painted black with manganese paint or slip to strengthen the animal shapes. This is characteristic of the high standard of work produced in the Aegean and north Levant before the unrest and destruction of the next two centuries. This is caused by the waves of invaders from the North who slowly moved down the peninsula; fighting, raiding, plundering. By the ninth century BC these various groups had begun to make permanent settlements in Greece, on the Aegean islands and the eastern Mediterranean coastline and become farmers and traders - and the people we call the Greeks. That is a later story in Tutorial No.6.
An early examples of a tile decorated with coloured glazes. The fragment here comes from Susa in Iran. It is thought to have been made during the eighth century BC but it could have been made much earlier c.1200 BC before the widespread unrest. We can see clearly that different coloured glaze materials have been applied and the black outline. Compare with the previous illustration and the earlier detail of a necklace.
This picture of a large decorated clay pot shows the next stage in glaze development: making up paste mixtures of soda, quartz powder and colouring oxide to brush or paint onto a tile or pot. This seems to have taken a long time to evolve and probably happened in Mesopotamia rather than Egypt. Unfortunately there is not enough accurately dated archaeological evidence to follow these developments closely. This vessel was found in the treasure of Ziwiye in Western Iran. It's exact dating is not agreed so it may be as early as the 12th century or as late as the seventh century BC.
Whatever the actual date, the quality of the decoration and glazing is evident in this detail. The body colour shows through the glazes when thin or not brightly coloured. These soda glazes are thin, transparent and fluid. There maybe a white slip under some parts. The principal colourant is still copper but the greenish blues may be due to added iron, from clay or sand, or just the body colour modifying the blue. A cultural link between this region and that of the Aegean is clearly evident in the style of the drawing of this bull - Cretan, Mycenaean, Archaic Greek. Some of the black slip line drawings on Mycenaean/very early Greek pottery are remarkably similar to drawings such as this - but without any coloured glazes. See my later tutorials.
From an Assyrian site this tiny pot is about three inches high and has the same "petal decoration" beneath the neck. The glaze here appears quite thick and opaque. The outline here is not dark but light. It seems that if the glazing technique did die out around the 11th or 10th century BC it had revived or was relearned by the time this pot was made three centuries later about 700 BC..
 |
Glazed Bricks - Massive Wall decorations in Western Asia
From earliest times, the people of Western Asia used bricks rather than stone for building. Simple sun-baked blocks at first but, as time passed, kiln-baked bricks were used for facing. These were often modelled or press moulded. This photo shows part of a temple wall constructed about 1450 BC in the ancient Mesopotamian city of Uruk. The figures represent city deities. The bricks have been press moulded and then assembled together to give the impression of a figure standing in each niche. Originally this wall consisted of a long row of similar life-size figures.
As the centuries passed, this style of wall decoration developed under the influence of the multicoloured frit paste tile work of Crete and Egypt. Assyrian, Babylonian and Persian craftsmen each in their turn used moulded bricks and tiles for their wall facings and contributed new refinements of their own in cities such as Nineveh, Nimrud, Babylon, Persepolis and Susa. Many have now been destroyed or have crumbled away. But large sections of a few glazed brick walls have managed to survive until recent times and are today preserved in the world's great museums.
Glazed Bricks in Assyria - Ninth Century BC
Nineveh in Assyria, Palace of Ashurnasirpal II (883-859 BC) Part of a square clay brick with a complete scene in black on a poor blistery white glaze. These early glazes on clay are very crude and show no sign of the perfection reached some 600 years earlier in Mesopotamia, Iran or Crete. it seem most probable that the craft died out in the twelfth century BC and was rediscovered or relearned in the eighth or seventh centuries BC.
Nimrud, Assyria. Large panel of glazed clay bricks from Fort Shalmar, representing Shalmaneser III (858-824 BC) beneath a winged disk. This is an early example of a large design built up of separate bricks. The black-line glaze is quite crude, with poor adhesion to the straw-tempered brick beneath.
A detail close-up of the head of one of the figures.
Glazed Bricks in Babylon - Sixth Century BC
After defeating the Assyrians, the Babylonians under King Nebuchadnezzar rebuilt the ancient city of Babylon. This impressive arch and processional way (now in Berlin) was built between 605 and 563 BC It was a massive structure faced with thousands of press moulded bricks covered with lifesize images of great lions, bulls and a variety of fabulous beasts.
The Great Gateway and this Processional Way were dedicated to their goddess Ishtar. These facing bricks are made mostly from quartz sand with some soda and colouring oxides. Very similar to Egyptian frit paste in fact. By this time potters in Mesopotamia had learned to make coloured soda glazes they could pour or brush onto these moulded bricks.
Many bricks have a life-size representation of real or mythical creatures modelled in relief. Against a background of peacock blue the creatures were painted in rich contrasting colours. A bright orange yellow was generously applied to the bulls and the manes of the lions. In bright sunlight they would appear to be made of gold.
Persian Glazed Bricks - fourth Century BC
Invaders and conquerors succeeded one another in Western Asia. In 538 BC The Babylonians surrendered to the Persian King Cyrus. His success in Babylonia led to a new era of Persian rule in the Middle East. The centre of culture moved to Iran but the imperial art and architecture continued the Mesopotamian traditions. The Persian ruler Darius 1 began c.520 BC a great palace near the site of the ancient city of Susa. His successors continued to make additions. The following examples from Susa were made sometime during the reigns of Artaxerxes II,(404-358 BC) and Artaxerxes III (359/358-338 BC).
Completed by Artaxerxes III, this is part of a long glazed brick panel which once lined the walls of the king's audience chamber. We see a procession of archers of the imperial guard in their impressive ceremonial uniforms.This tile work dates from about 405-362BCThere is a superb range of colours using copper, cobalt, lead and antimony.
This detail show how all the elaborate ornament has been captured in clay and glaze. The Assyrians and Babylonians had used a sandy clay brick, now the moulded brick material seems to be something akin to the quartz paste used in Egypt with a whole network of ridges made by slip trailing this glassy body and then painting the hollows with copper, manganese, iron and cobalt minerals and soda. These bricks were fired at not much over 900'C.
From the Palace of Artaxerxes II,(404-358 BC) Susa, this detail of a Griffon(fabulous composite creature) from a long frieze shows a more stylised form ,dynamic line and greater drama in these creatures. Compare with the earlier Babylonian lion reliefs. By the fourth century the colonies of Asia Minor, Egypt and Phoenicia were part of the Persian Empire and these foreign influences are reflected in Persian Art.
Two Assyrian Glazed Brick Fragments.
This brick is a very coarse sandy body. The piped or trailed raised lines or cloisons separate the coloured glazes in the petals of the rosette. These can be seen quite clearly in this fragment. The glazes are only lightly applied here and hardly cover the sandy buff body.
This brick is a fine grey/white quartz frit body. The fluid but thick glazes seem to cover up some of the detailed linear patterns and much of the colour seems to have leached away.
Glazed Brick Fragments - Harrow Tutorial Research Project. Two of a series made by B.A. students to test possible recipes for Persian glazed tiles together with Making and Firing Techniques.
Illustrating a possible way frit body mixture could have been piped to produce the raised lines on the frit body tiles.
Showing how very fluid coloured glazes can be easily separated by these piped lines or cloisons.
Email me if these tests interest you.
|
 |
The Middle East after the Conquest of Alexander in 330BC
There isn't yet a definite explanation for why the technique of glazing bricks vanishes from Western Asia with the conquest of Alexander c 330 BC But it is significant that none of the earlier Greek city states nor their colonies had been much influenced by the colourful ceramic tile work that reached such high standards in contemporary Persia of the 6th, 5th and 4th centuries BC Alexander built cities in the Greek style without ceramic decoration.
This is a large decorative jar from the Ptolemaic period, probably 2nd century BC. It is made in blue frit paste, moulded in pieces and joined together. The press moulded handles were then added. There are no hieroglyphic motifs, its only decoration consists of vertical grooves shaved into the pot walls. The surface is quite glassy and could have been covered over with a soda glaze to heighten the gloss and the colour. In this late Egyptian period they had become extremely skilled in using frit paste. Alexandria, the new capital, soon became the most important centre for fine glassware and remained so for many hundreds of years despite all the political changes.
Egypt gradually became Hellenised under the line of Greek pharaohs descended from Alexander's follower Ptolemy. There was a gradual blending of the Egyptian schematic with the ideal naturalism of Greek art. Glass and frit paste manufacture continued down to Roman times, but classical Greek ideas and motifs gradually replaced traditional Egyptian patterns and religious imagery.
This jug from second century BC Egypt has a distinctly classical Greek quality. It appears to be a thrown jug in a pale clay body and the rim alterred to produce a distinctive Greek type lip. The classical style draped female figure in high relief is sprigged or pressed on with a mould. The pot appears to have been brush painted with a thick soda glaze mixture based on pale blue frit paste. Where thin the buff clay body has that toasted burnt look often caused by soda.
This extraordinary piece from Alexandria in the second century BC is made in a very glassy form of frit paste. There are two subtle shades of white/grey paste used to create the effect of feathers on the goose's body. The imagery is based on a Greek legend. The winged boy infant a classical prototype which has lasted down to our own time. Only expert craftsmanship could achieve such results out of so difficult a medium and it doesn't survive and develop in the Roman world. This was probably because, with the invention of the technique of glass-blowing about this time, similar hollow objects made in coloured glass became much easier to make than frit paste.
The Possibility and Concept of a Glaze is Established
During much of the second and first millennia BC, potters in Mesopotamia, Persia and the eastern part of the Mediterranean had been experimenting intermittently with the techniques of glaze brushing and pouring. Accidental discoveries led to brushable glazes by the Assyrians and the Persians before 1000 BC But, from the evidence of pots and glazed bricks and tiles found all over the Middle East, the secret of glazing seems to have been discovered, then lost or destroyed and relearned again during the first millennium BC - down to the Roman era and perhaps beyond. As we all know, making glazes can be fraught with problems, so it is not surprising that the real understanding of the nature of glazes and glazing eluded these ancient Egyptian, Babylonian, and Persian potters. The situation however was changing; by 300 BC many middle eastern potters knew that the idea of a brushable, pourable glaze was a possibility even if it was a problem to find the correct ingredients and a struggle to perfect it.
At Last - Low-fired Glazes for Clay Pots
Potters in the East(Han China) and the West(Roman Middle East) were developing alkaline glazes from mixtures of soda ash, wood ash, powdered glass, fine sand, clay and colouring oxides with enough water to make a paste which could be brushed or poured onto raw clay pots to producing a shiny coloured glazed surfaces when fired to below 1000°C. During the 1st-3rd centuries AD the technique of glazing more expensive and decorative ware was spreading both in the Western Roman World and eastwards across Persia and Western Asia. In some areas potters also realised the value of lead compounds in a glaze. At about the same time in the Far East low temperature glazes also began to appear. See my later tutorials.
In the early centuries of the new millenium AD., potters in Iran(Parthia) were using an alkaline copper blue glaze brushed or poured over clay pots. Items as large as clay coffins with decorated lids, as in this illustration were being made press-decorated, poured or brushed with an alkaline copper glaze and then fired.
This alkaline glazed vessel with the roughly stamped classical figures on the neck was made at the Eastern edge of the Roman World in Parthia(Iran) during the 3rd century AD.
This goblet of red terracotta clay is decorated with modelled naturalistic leaves and slip trailed or piped decoration. The warm green colour with its smooth glossy shine suggests it was brushed or dipped in a glaze containing lead as well as soda. The complex naturalistic applied decoration with the limpid, craze resistant quality of a lead glaze was a clever way to compete with the important glass-making industry of Roman times. This little decorative cup was found in Corinth. Dated first century AD.
Postscript:
To end this tutorial, I can do no better than quote the Chartered Surveyor, Mining Engineer and Archaeologist John Dayton who writes at the beginning of his introduction to his book Minerals, Metals, Glazing & Man, "The origins of glazing are lost in time..." But then goes on to tell us so much about these origins and background. Whilst writing this tutorial, I have unfortunately discovered that this fascinating book is out of print, so you would have to look for a copy in libraries. It is worth the search though for anyone who gets hooked on this subject and would like to explore early glaze history more deeply. The ISBN number is: 0 245 52807 5
Summary: Tutorial No.4. Quartz Soda frit and Early Glazes.
Origins of glaze and glazing lie in the prehistoric metal and mining communities of Europe in the third millennium BC rather than Egypt or Mesopotamia.
The first man-made glazed objects were fragments of self-glazed blue frit quartz paste, followed by drilled beads made of blue frit. Soon after 1900 BC the technique was being used in Crete and a hundred years later had spread to Egypt and Syria.
The Minoans on Crete c.1800-1300 BCseem to have been the first to exploit the full decorative possibilities of this colourful self-glazing material. They were probably the most innovative craftsmen in the ancient world. Unfortunately surviving examples from the Aegean are all in poor condition due to the damp tombs.
Initiated and aided by Cretan craftsmen, the Egyptians of the 18th Dynasty, particularly during the Amarna Period, c.1372-1362 BC, produced some of the finest pieces of multicoloured frit paste - much of it jewelry. Protected in the warm dry tombs many good examples have survived.
The Cretans were the first to make coloured inlay panels and a soda frit glaze to paint on pots, but by the end of the second millenium tiles and inlaid panels of coloured frit were being made in Egypt and Mesopotamia.
Soon after 1000 BC brushed and poured soda frit glazes begin to appear on some pots and bricks in parts of Persia and Mesopotamia. By 500 BC coloured soda glazes had been made in Assyria, Babylonia and Persia to decorate moulded bricks. These were often built up into magnificent palatial wall decorations, both dramatic and colourful.
With the Conquest by Alexander the Great the whole region became gradually Hellenized. For some centuries the exuberant rich coloured glazes on pots and brickwork were mostly replaced by classical motifs and the muted colours of unglazed red and black terracotta pottery.
In Ptolemaic Egypt, monochrome frit paste pale blue or off-white pearly colours became fashionable.
Glazed pottery survived in the Eastern past of the Roman Empire but was never widespread. In the Western part of the Empire there was very little. On the edges of the empire in Western Asia pale blue/green glazes gained a small foothold and the technique managed to survive quietly for several centuries eventually to flourish magnificently in the Islamic world.
By the closing centuries of the first millennium BC Low temperature alkaline glazes were being used on some clay pots. The use of lead in glazes begins. By the time of Christ, alkaline and lead glazes were being used in the Roman world and the Han dynasty in China - both the subjects of later tutorials.
| |