 |
Victor Bryant ©1994,2011
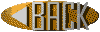
To Index Home Page
Ceramic Web Page Tutorials
[
11
]
(Chinese Ceramics 3.)
Early Imperial China ca. 200BC to 600AD
During this long eventful eight hundred years the style and character of Chinese Ceramic Art was born.
by Victor Bryant
Last added-to or revised 31 Jan 2011 V.26.3
PART II Tutorials 1. - 8. CERAMICS IN CHINA
|
 |
 |
If you just want to see the ceramics or make a quick survey of the images:
Scroll down through this main text page,
click on a thumbnail image which interests you;
a larger image will appear in the left frame.
-More Info
-Picture Reference
|
 |
 |
 |
Prologue:
In 206BC the (Ch'in) First Emperor, Shi Huang died. His vast project of producing
a lifesize terracotta army for protection in the next world serves to remind us of the unparalleled bronze and ceramic skills and expertise available in China at the beginning of the Han Dynasty - an army of trained craftsmen modellers and mould makers.
Though essentially sculptural rather than pottery techniques, mould making methods did have a strong and continuing influence on later Chinese ceramic forms. I have included the following section on Han terracotta sculpture because of its quality and influence.
Depending on size and complexity, clay figures were usually press-moulded in a number of parts. A small range of heads, arms, legs and bodies would enable a range of similar but not identical figures, which could be further expanded by varied painted finishes.
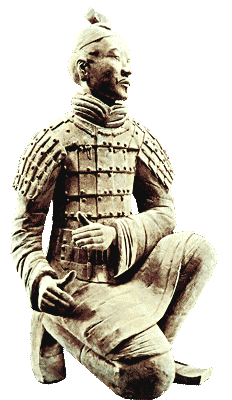 |
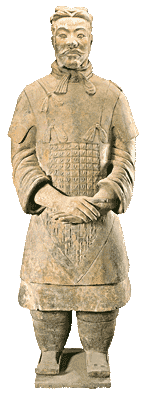 |
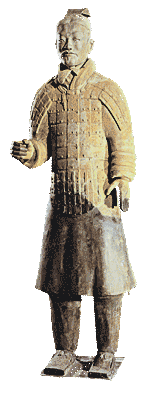
Three of the near life-size soldiers
|
Making these Terracotta Warriors must have needed thousands of skilled craftsmen to achieve such a project - model-makers, mould-makers, kiln-builders, fireman etc. This was ceramics on an industrial scale never before seen. With the enormous number of press-moulded lifesize clay figures in mind, imagine the size of the factory workshop site and the breathtaking collection of kilns being fired!
|
 |
Han Terracotta Sculpture and Pottery
Western Han(ca.206BC-24AD)
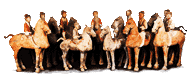
11001 Cavalry with painted decoration. H:68cm. W.Han Dyn. 206BC-9AD XMC.
|
|
|
 |
Foot soldiers and Cavalry in Clay
11001a Two miniature soldiers on horseback. H:48cm. W.Han Dyn.206BC-9AD XMC Two horses with their riders from the collection above. The restrained calm naturalism shown here is characteristic of such figures from the Ch'in and Western Han tombs. The details of the face, clothes and fittings are clear and sharp but never over-refined. The elegance and 'stillness' has parallels in other cultures - for example, Early Egyptian, Early Greek, Etruscan or Early European Renaissance sculpture.
11013 Horse and rider. W.Han.Dyn.206BC-9AD Han Emperors were constantly defending their northern borders against the hostile tribes of warrior horsemen across the Steppes (Huns, Mongols and Turks). The military strength of the Han dynasty lay in its bureaucratic structure, advanced weaponry and the speed and endurance of a new breed of horse imported from the Western reaches of the Silk Road. A well-trained cavalry was vital. They bought and bred many different breeds of foreign horses in their attempts to produce a superior battle horse. This obsession with horsebreeding and cavalry perhaps explains the vast number of such models found in the tombs of Han Nobles. Tombs belonging to Han military officers often contained replica cavalry and footsoldiers fashioned from clay. As many as six hundred mounted cavalry soldiers similar to these examples were excavated from the tomb of the famous Han general Chou Po in 1956 near Hsien-Yang in Shansi province.
11014 Two miniature painted earthenware foot-soldiers. H:48cm. W.Han Dyn.206BC-9AD. The modelling and painting of these two minature footsoldiers accurately depicts the military uniforms of the early Han period. One wears a chest protector of leather or metal armour and both have high boots and thickly padded clothes
The collars and sleeves are expecially bulky, to give some protection against arrows and other weapons. As in the last image, each soldier held bronze tipped weapons which are now missing. The red ribbons may have indicated some rank.
 11044 Harnessed horse press-moulded in earthenware with applied colour painting 6th.C. AD. Wei Dyn Northern China. H:15cm GMP. Well-proportioned, lively idealised clay images such as this were an important element in well-furnished aristocratic tombs onwards from the 2nd to the 6th century AD. The detail from the back shows fairly clearly the the hollow press-moulded shell of the body with separate press-moulded legs added on.
.
11037 Model bronze flying horse H:24cm Eastern Han dynasty 2nd C AD. The new breeds of horses brought into China from central Asia during the late 1st century B.C., were larger, stronger and faster than the native chinese horses and rapidly became the image of power and prestige. This spirited bronze flying horse, standing by one leg on a swallow in flight, epitomises this blend of ideal and real in its modelling; it captures the spirit of the fabled celestial horses of the Han, and is good example of the conquest of movement and naturalism in Chinese sculpture during the 1st - 2nd centuries AD. Potters would have admired this piece and probably copied it.
|
 |
 |
Bronze forms often copied in Clay click 
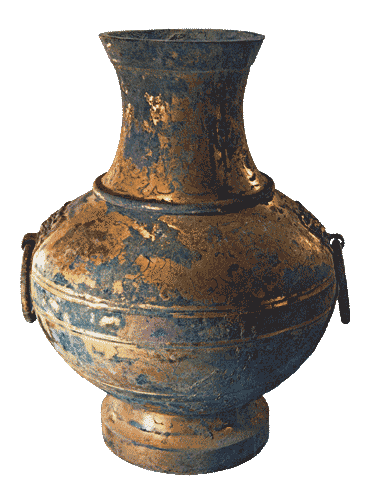 11046 Gilded bronze wine vessel chung. Western Han 206BC-24AD Changan, Shensi
|
 |
Early Han Painted Funerary Pottery
(Western)Han period(ca.206BC-24AD)
|
|
|
 |
During the early part of the Han dynasty 'cold' painted or lacquered earthenware ceremonial vessels, instead of bronze, appear in tombs. It may be that bronze was becoming too expensive or scarce. Ceramic vessels were certainly a much less costly version of a bronze form. A desire for more colour and changing fashions may also have played a part.
11033 Painted earthenware ceremonial vesselhu. Western Han Dyn(206BC-24AD)Loyang, Honan. The fired body of this lidded funeral vase appears to be a dark grey. In order to prepare it for painting, it was first covered with a white chalky or clay pigment probably using glue to give a smooth painting suface. A small range of colours and patterns echo some of the richness of bronze inlay patterns. The bright red may be restoration but originally it would have been red iron oxide or possibly lead or mercury oxide.
11031 Another large Painted Funeral Vase hu. 2nd-1st c BC Western Han Dyn.GMP 11032 Detail of 11031. This grey earthenware vase has been decorated to imitate a black lacquer finish using lighter coloured linear swirling patterns.This detail(right) shows one of the two press-moulded "monster" lug plaques - imitating similar fittings on bronze vases.
11020 Another large Painted Funeral Vase hu. 2nd-1st c BC Western Han Dyn.GMP 11021 Detail of 11020. Another similar painted earthenware vase is somewhat better preserved. The colours used here include many expensive powdered minerals such as lapis for blue and perhaps red from mercury or lead minerals and copper minerals for bright greens - all this in addition to a range of ocherous clays for softer yellow reds or browns. White from clay or whiting for those sparkling touches and lighter coloured linear swirling patterns. The detail(right) shows similar designs to those found on bronze vases.
11029 Ovoid earthenware lacquered flask. Western Han Dyn 206BC-25AD. H:27.5cm. 11030 Detail of lacquered flask. A beautiful ceramic piece made from two thrown bowls joined at the rims, then a thrown neck and foot added. When finished it fired to a smooth grey form which imitates the form of the silk-worm cocoon. The technique of lacquering on ceramics is much rarer than on wood. This was decorated with layers of silver and red coloured lacquer and a final intricately drawn design in black painted on top. Though not easy to see because so dark, the design is a complex pattern of stylised and intertwined phoenixes and serpents. Its survival in such good contition is due to its resistance to dampness.
11026 A painted ovoid earthenware vase, hu.Western Han Hsinhsiang,Honan. GMP. Like the cocoon form above, a vase essentially made by expert throwers and the two bowls joined into an elongated globular form. The thrown foot and neck were then added and, after drying, probably covered with a smooth white slip before firing. The bold stylised design using limited gum colours combines with the sharp ovoid form gives this pot great visual strength.
11007 A press moulded, painted grey earthenware vase, hu.Western Han Hsinhsiang,Honan. GMP. 11008 Detail of painting above. Now a hand built press moulded vase which when fired has been painted in bold patterns and contrasted colours. Such shapes need careful building and joining if they are not to distort, split or crack. These craftsmen were clearly experts. The bold contrasts in tone and quite limited colour are expertly brushed into swirling patterns producing a sparkling design with deft touches of white.
11028 Painted Grey Earthenware Western Han Ht.45cm. 11028a Detail of pic above. Another grey earthenware vessel afterwards decorated with painting after firing. The potter/painter here uses a greater range of post-firing gum/tempera colour and the body of the design is now quite naturalistic, with both fine brush-painted lines and scrafitto(scratched) to give detail. The technique appears similar to the gum/colour painting used by the Greeks. To refresh - re-read Tutorial 6 - Painting on a White Slip Ground - an example of parallel but independent experiments producing similar solutions.
|
 |
 |
Ceramic Achievements of The Early Imperial Age
1. Stable lead glazes, coloured with iron or copper.
2. First stable stoneware glazes (clay/ash/lime).
3. Kiln technology now the most advanced in the world.
3. Pottery-making becomes an major industry.
5. Before the end of this Age, fine ceramic pieces were recognised as Fine Art.
|
 |
Han Lead Glazed Earthenware

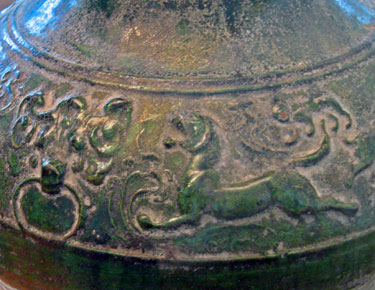 Press-moulded earthenware covered with a low temperature glaze Fluxed with lead oxide plus iron or copper oxides
|
|
|
 |
11047 Lead-glazed Po-shan-lu jar with cover E.Han period H:24.1cm VAL. The cover of this jar depicts sacred mountains populated with animals of Han mythology, mainly dragons, tigers and bears. Around the main register is a landscape scene with hunters on horseback pursuing wild animals.
 (Left)11036 Info about pic here.(Right)11055 Info about pic here. Such jars, Lien, were used to store small items, especially cosmetics. These examples show the variety of results achieved with iron or copper in the lead glaze - plus the effect of different bodies underneath. The mountain peaks in all these examples seen here are also represented more grandly on the lid of the bronze censer po-shan-lu. This "Mountains of the Gods" symbol was inspired by popular Taoism and its fixation on immortality.
 |
Lead Glaze decay
Like all low temperature glazes, lead glazes are vulnerable to attack by water-soluable minerals and even the weak acids found in rainwater and soil. Lead glazed pots in a damp or water-sodden tomb or grave would soon be affected and gradually lose gloss and colour. The results of this decay over centuries are often quite surprising and frequently attractive. Here are some Han examples.
|
 |
 11099B Info about pic here. 11056 Info about pic here. This lien jar was made from a clay which fired a pale warm buff colour(look at the unglazed part of the feet). It is covered with green(copper) lead glaze. Almost certainly due to the damp or wet conditions over centuries the rich apple green colour has been affected to different degrees producing a variety of irridescent colour changes.
 11054 Info about pic here.11053 Info about pic here. Two examples of green(copper) lead glazed Han earthenware. The glaze has rotted away most if not all of the green colour leaving a frosty iridescence.
11057 Info about pic here. This Han Lead glazed earthenware candelabra or censer was originally covered with a rich green lead glaze. Today the frosty mottled sheen of the rotted glaze looks almost like old silver. In some parts, you can just glimpse the light terracotta colour of the fired body underneath, particularly around the foot where the glaze has completely flaked off.
Han Earthenware Models (sometimes lead glazed)
11012 A model of a tower or pavilion in earthenware. H:33cm. orig. green lead glaze W.Han Dyn. 1st-2nd c. AD. Ceramic models of common structures were often placed in tombs during the Han dynasty. Improved methods led to the construction of many tower-like buildings made of brick, wood and ceramic tiles. Since none of these esentially wooden buildings have survived such detailed models allow us to understand a lot about ancient Chinese architecture. This model is made up of five detachable sections which together form four levels. Although nearly two thousand years old, it clearly shows the cantilever bracket system of these wooden-tiled roof towers with deep overhangs and walled courtyards which have remained standard in traditional Chinese architecture to the present day. This basic system of multi-storey construction was later adapted to the building of Buddhist pagodas.
 11058 Info about pic here.11058a Info about pic here. This is a more elaborate model but similar in structure. Modelled in red clay, it was covered with a copper lead glaze which has rotted considerably producing this mottled multi-coloured effect, particularly where the red body colour shows through. The two image details show the amount of care taken to model architectural features and figures.
 11060 Info about pic here.11060b Info about pic here. A somewhat less ormented tower is indicated in this model. The red earthenware bowl which forms the base suggests a farm duck pond of Han gentry rather than an aristocratic estate. Most Han gentry lived in relative luxury and hoped to live equally well in the afterlife. They commissioned clay models of their mansions, granaries, mills and watchtowers as shown here.
11042 Info about pic here. 11043 Info about pic here. These two models show the working side of such an estate and include quite an amount of detail. On the left, a pig sty. It houses a sow, suckling pigs, boar, roosting chickens and dog, the pen is connected to two latrines. Tiles line the tops of the walls and cover the hip roofs. Combination pig sty-latrines similar to this replica can be seen in many parts of rural China today. The model illustrated on the right provides a good representation in clay of Han cooking facilities needed in the next world.
|
 |
Perhaps the most important ceramic achievement in the First Imperial Era
was
The First Stable High-Fire Glaze
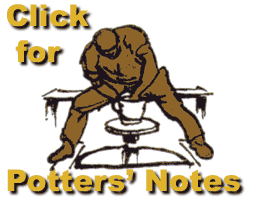 The Basic Requirements
 |
Now follow the stages of the development of the first stoneware glaze - from accidental glazing on Shang and Chou pots to glazed stoneware masterpieces in the sixth century AD. by examining my examples of chinese pottery in sequence from Chou times to the approach of the T'ang Age.
|
|
|
|
 |
STAGE 1 Accidental Glazing in the Shang Era
In Shang China enormous moulds and models of refractory clay were being fired in vast quantities in the bronze foundries - see Tutorial 10.
Kiln walls eventually become
glazed After long and regular exposure to wood firing at temperatures of over about 1160°C a progressivly increasing shine or gloss would cover walls and fireboxes as the potash and calcium fluxes in the wood ash dust were carried through the kiln from the fire chamber to vaporise, decompose and attack the surface clay of the brick walls to produce a glaze.
No written evidence Chinese scholars from Shang to Han times have left us little evidence of the slow but enormous developments happening to our lowly craft during Shang, Chou and Han times. Such a craft was of little importance to scholars and was probably too hot, dirty and smelly for such exalted people to get near!
Accidental glazing on Shang stoneware
Accidental wood ash glazing must have happened in the kilns used in the Shang bronze industy. Droplets of glaze have been found on the shoulders of Shang pots.
Below are some examples of Shang and Chou pots illustrating this phenomenon showing drips of molten glaze from the kiln roof on stoneware pots. We have no idea of the exact circumstances, kilns or firings, except for the dramatic evidence of these glassy glaze drips on a number pots dated from the Shang era. The examples below were shown and commented on in detail in Tutorial 10. But remember to use to return to this tutorial.
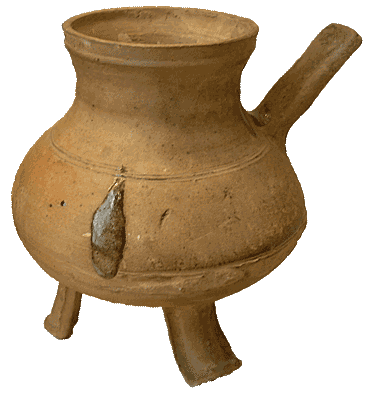 1019
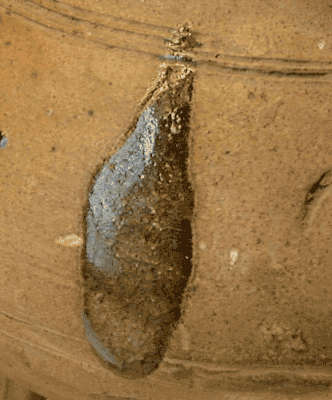 1020
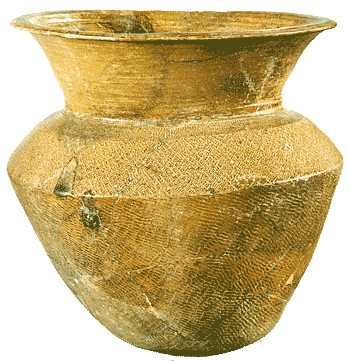 1021
Shang stoneware shown in Tutorial 10.
The exposed parts of the clay pots or moulds would become shiny or even thinly glazed if fired in well-used (and heavily glazed) kilns. But all this accidental glazing would depend on the stacking and packing of the kiln as well as the amount of glaze already deposited on the walls.
|
 |
|
|
|
 |
STAGE 2 Haphazard Slip Glaze Experiments during Chou Era
The Earliest Stoneware Glazes This next stage came with an understanding of the cause of the glaze and how to encourage and eventually produce it at will. Discoveries of pots from the early Chou period, occasionally appear to show that potters had begun to brush on, pour over or dip pots with clay slips and woodash to produce a shine(glaze). Making a glaze from clay slip and woodash and lime may at first appear a simple problem because we know it can be done, but in reality, discovering or inventing the first high fire glazes became a long series of local explorations after many accidental discoveries - and probably many failures over centuries. There is no continuous glaze development from Shang down through much of the Chou era. These examples from the first half of this era illustrate how chequered a journey it was to produce a useful stable stoneware glaze.
Our certain knowledge of how early high fire glazes developed in China is not so clear. Over many centuries and different regions during the Chou Age, there seem to have been a pattern of accidental discoveries, haphazard and spasmodic attempts to produce a glaze which is soon forgotten - examples above. There is no evidence of continuous development until the late Chou Age. Examples of high fire glazed stoneware have been found in various locations in the earlier centuries of the Chou Age but these pieces are variable in many ways as seen in the examples below: form and making styles, glaze colour and quality. There is as yet no coherent pattern of high fire glaze development.
Early Chou Glazes Eveentually during first centuries of the Chou era some Chinese potters at various times and different places began to experiment with simple mixtures of common clays, ashes and common minerals such as lime or whiting to produce a smooth shine or a glassy film of glaze on their stoneware pots. The varying pottery styles and glaze results can be seen in the following examples: greenish-yellowish-brownish-greyish glazes depending on the recipe, firing and the local materials.
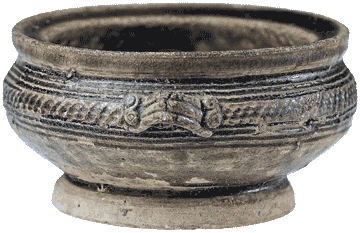 10112,1043,1044,10125
There seems no link between the forms either. Such glaze exploration appears to have been sporadic and without any continuous development until much later in the Chou era.
The Early Chou pots above were shown and commented on in detail in Tutorial 10. But remember to use to return to this tutorial.
|
 |
|
|
|
 |
STAGE 3 Another Start from Scratch in the South-east
during late Chou and Han Eras
The Genesis of the Yüeh Glaze(s) Based on Clay/Woodash/Lime Fired in Cave and Climbing Kilns
The real (continuous) development of high-firing ceramic glaze in China began in the Zhejiang/Fukien provinces before the Han. It was based on the local cave kilns - simple to construct and capable of high temperatures; the plentiful local stoneware clays; and an ample wood supply provided by this hilly, forested region, known in ancient times as the Yüeh. This seems to have been where high-fire glaze and kiln development continued through generations of potters for hundreds of years.
These late Chou stoneware pots below are covered with impressed patterning. The first has no other treatment, but the other two have been covered with a darkish slip probably containing iron. One brushed and the other dipped. This slip has melted a little producing a soft shine.
The Late Chou pots above were shown and commented on in detail in Tutorial 10. But remember to use to return to this tutorial.
By the late Chou period potteries in Zhejiang/Fukien and south eastern coastal regions are producing quantities of high fire grey stoneware which were probably self-glazed by wood ash blowing through the kiln, but by Han times are partially glazed. We can only speculate about the composition of these earliest slip glazes applied to
leatherhard or dry stoneware pots but I am certain they can only be woodash and/or lime mixed with clay slip.
High-Fire Ceramics in the Early Imperial Era
First and second centuries AD
11061 Stoneware Storage jarpou. Jiangsu Province ca.1st c.AD. E.Han Dyn. 11062 Detail of pic above Many jars like this have been found in Han Dynasty tombs in eastern China, Jiangsu province. The slight glazing of the top third may not be a thin wash of wood ash or lime but produced by vapourised flux material (from the wood ash blown through the kiln) attacking the surface clay particles and producing a glaze. In fact, the presence of this thin "oily looking" deposit tells us that this pot was fired in excess of 1150°C. because wood ash would not begin to melt and vaporise at lower temperatures. The deeper grooves around the lower half are the result of smoothing exessive throwing ridges using a wooden or bone rib tool.
These storage jars often appear to have been made by joining two thrown pieces: 1. A deep bowl base, 2. A shallow bowl, inverted to form the top, with a hole cut into the centre. This forms the globular pot as illustrated here. When leather hard, the two bowls would be luted or joined together with a little clay slip. On a wheel, the upper part was the smoothed with a rib and the three bands of fine combed ridges. The simple rim would be marked out raised, smoothed and finished on the wheel. Finally the lug handles (made in a variety of ways) were luted on. As can be seen in the detail, a stylized little creature has been pressed out and fixed on. Above it is a tiny double spiral roll of clay. A frog with a worm? Is this deep symbolism or just humour? These pots seem to contain a blend of influences; sturdy utilitarian ceramic forms combined with sombre toughness and figured lug handles echoing a bronze ceremonial bronze. There was clearly a market for such stoneware funerary vases. Many have been found in burial sites.
11063 Stoneware Storage jar. 11063a Detail of pic above. This stoneware vase was made in a similar fashion but it has a more flattened globular form, a flared foot, a tall flared neck with an everted rim (which becomes a common type of rim). The rings of fine combed ridges are similar, there is also a decorative band of wavy scratches near the middle of the vessel. Here there are only simple pulled lug rings. The surface has a similar thin deposit of ash/lime glaze. This pot is perhaps more bronze-like than ceramic in form.
|
 |
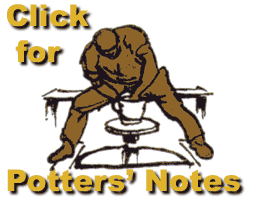 Food for Thought: Historical & Technical Information
|
|
|
 |
STAGE 4 A Stable Stoneware Glaze with a simple recipe
Early or proto-Yüeh type glazes By the end of the Chou era, it becomes clear that the main centres of producing grey stoneware were in the coastal south east region and that the simple cave and hill kilns have evolved into larger more efficient climbing kilns. The ancient name for this region was Yüeh and it has given its name to a broad group of clay/lime glazes produced in this region from late Chou or Han times.
Limited Glaze Materials and Simple Recipes Local grey clay, chalk/limestone/lime plus wood ash (and sometimes red clay) were the readily available local materials. Using simple proportions of two or three materials, stable glaze recipes were arrived at by chance or trial and error over a long period. From such simple glaze recipes combined with different firing cycles, a surprising range of high fire glazes were eventually produced.
Glaze and Firing Secrets There were of course no ceramic text books to refer to, but probably many secrets about firing techniques and glaze making were passed down from fathers to sons. The recipe for the Han glazes below was probably about two parts of clay to one part lime plus a smaller amount of ash. Read a fuller description of these glazed pots further on in this tutorial panel.
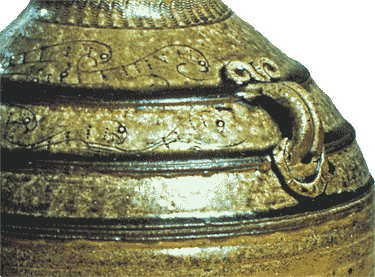 11065
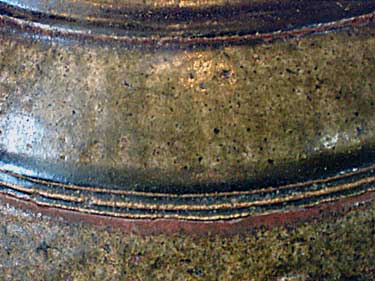 11068
Details of Han jars 11064 & 11067 shown in this Tutorial 11.
A Stable High Fire Glaze Achieved A highfire glaze made from a few common materials was now clearly possible. Yüeh potters continued to refine and modify their simple glaze recipes and firing patterns. They also began to use finer and paler clay bodies.
11067 Proto-Yüeh Glazed Stoneware vessel. Eastern Han dynasty With a stoneware pot like this one feels that there is a fresh spirit at work in the Yüeh workshops of South Eastern China. Essentially a thrown stoneware domestic pitcher for wine or water; a generous globular form with a fine flared lip for filling or pouring, but the finish, and glaze show us that it is not an ordinary kitchen pot. The brushed glaze is made from a mixture of clay slip, ash and lime; the simple recipe arrived at by experiment. The three raised bands or cordons were built up as ridges to collect excess glaze and so prevent most of it from running down and disfiguring the the pot, although at least one ridge probably indicates the join between the parts which make up the pot.
11068 Detail of glaze.The detail shows clearly the chacteristic shiny black colour above and between the tiny ridges and the dry red iron colour below the bands, which indicate to an experienced potter that these ridges have been brushed with an iron oxide or red clay slip. The dull frosty grey green colour is typical of such ash/lime glazes, as is the slight oily quality. Iron and lime contribute to the greenish colour of high temperature glazes fired in reduced (smoky) atmosphere kilns. With a lot of iron present in a thick glaze the colour can become brown or black. If, on the other hand, the glaze is thin and a lot of iron is present, then, as the kiln cools, the excess iron compounds oxidize and become a frosty red - hence the colour differences around the ridged bands.The body contains some iron. Under some reduction atmosphere in the firing, you would expect the fired body to be a cold grey but, on cooling, iron particles on the clay surface are reoxidized to red, so the body outside looks toasted not grey. However, within the dense stoneware body any iron oxide remains reduced and black, so the fired body will be cold blue-gray inside.
11064 Proto-Yüeh glazed stoneware jar. Eastern Han dynasty This must have been a very popular funerary vessel. A number of similar but slightly differently fired and/or decorated storage jars can be seen in various museum collections. This particular version shows clearly an incised decoration beneath the glaze; scratched, spearlike bands of combing at both ends of the neck. The neck itself is emphasized by being unglazed, as is the lower part of the pot. After scratch decorating, the mouth of the pot was dipped in glaze.
11065 Detail of glaze bands and lug handle.The incised decoration beneath the green glaze can be seen more easily in this detail. As in the previous example there is iron painted on the cordon ridges. This lug handle may echo the bronze handle tradition but this is definitely not imitating bronze, the rolls of clay are a step away from bronze; but the scratched linear patterns are echoes of bronze engraving as are the sombre colours of the glazes and bodies. Han pottery hasn't yet escaped the influence of the forms or colour of the earlier material, but Chinese Yüeh potters are slowly developing a ceramic style of their own.
|
 |
|
|
|
 |
The New Type of Kilns developed in South-East China: Cave kilns to Climbing kilns
The great advances in high-fire glaze and kiln development made in the south-east coastal regions were gradually passed on to other regions of China and also Korea and Japan. Key to high-firing ceramics was the evolution of the cave kiln into various climbing kilns (simple, long cross-draft and multi-chamber down-draft)
The Climbing Kiln (Note: My simple diagrams illustrate only the main outlines.)
The cave kiln was first translated into a simple tunnel-like clay form on a hillside in late Chou or early Han times. We have already seen pictures of Han stoneware fired in such kilns. High-fire ceramics continued to flourish and develop in the south eastern coastal provinces after the collapse of the dynasty. The simple, but effective, cave kiln had by then evolved into a mud and brick hillside climbing kiln. Over the next centuries this single chamber kiln evolved into a variety of kilns.
The most striking version was undoubtedly the dragon kiln, so-called because, especially as nightfall approached, it had the appearance of a monstrous undulating creature climbing the hill with flames and smoke spurting out of its sides and at the top a flaming mouth. This long single chamber climbing kiln and its variants were the foundation for an industry which developed in the villages along the southern banks of the Yangsi river estuary and on towards Hangzhou. The forested hills provided the fuel and the local stoneware clays were plentiful. Protected from the northern cavalry, by a vast river system and a strong navy, these southern pottery villages were relatively stable and prosperous for centuries
A later great refinement was to divide the tunnel into separate "down-draft" chambers. It then became a multi-chambered climbing kiln which was much more efficient to load and unload with each chamber separately bricked up. Using such kilns, mass-production of glazed stoneware pottery became an ever expanding industry.
|
 |
|
|
|
 |
STAGE 5
The Yüeh Clay/Lime Glazes South Eastern China
Glaze Testing and Kiln Control Altering the amounts of each ingredient in a glaze recipe and observing any changes on the fired ware isn't rocket science, but it needed accuracy and careful observation of the whole process to establish cause and effect. Only by careful repeat recipe measurements and repeat firing patterns and cycles over months or years could one hope to produce approximately similar results from each firing.
 11109 (Lidded) Stoneware Jars with doubleband lugs and sprig lion masks(Proto-yüeh) Late 3rd C. AD H:21cm. Typical pale grey body material which generally burns a reddish brown when unglazed. The glaze on these pots is thin translucent with a soft gloss. The small amount of iron in the glaze and body produces variable shades of pale brownish yellow to grey green, depending on the success of the reduction firing cycle and the thickness of the glaze. Usually such pots are glazed by pouring or dipping.
A simple 2:1 clay/lime glaze recipe
This was probably used to produce the transparent/translucent greenish glaze on the light-grey bodies of the two jars above. The simple recipe being 2 parts clay to 1 part lime and maybe a little woodash. Firing: about 12-1300°C atmosphere: neutral/reduction.
Refining the yüeh glaze took generations
It maybe took a few generations to be able to produce a particular quality of glaze: it would also need some understanding of how small changes in a recipe or firing pattern produced a range of different qualities of finish. Each village or kiln site probably used similar local materials and firings and therefore produced somewhat similar glazes, but another village or kiln site might produce a different range of glazes if their firing schedules were different,even though using similar glaze ingredients.
A range of glaze finishes in every firing
In fact, any kiln would produce a range of fired glaze finishes from the same applied glaze - something every experienced potter learns to accept. So - shiny, satin, stony or matt finishes and colours from pale buff through to orange patches with grey olive greens might be produced from the same glaze in a single kiln firing. With repeat firings you would therefore have a repeat range of finishes - customers love to have a choice! The pot below was probably glazed with a similar clay/lime type recipe but slightly different firing pattern
11072 Chicken-headed ewer Yüe ware.second half of 4th C AD H:23cm BML. The smooth grey-green glaze is marked with dark-brown spots from iron in the body. Red iron slip was brushed on the Chicken's eyes, comb and the lugs and around the rim. Many have been found in sites in the south-eastern provinces Eastern Jin dynasty 317-420
|
 |
 |
STAGE 5a
The Yüeh Clay/Lime Glazes Simple Recipe Variations
Probably more Lime and lower temps The glaze has a smooth stony surface. The glazes here are probably higher in lime compared with the previous examples.
 11107 and detail. Globular jar with wide ribbed rim. yüeh stoneware Eastern Han Dyn 2nd or 3rd C. AD. Shangu Kiln, Zhejiang Province H:27cm. The style of the wide rim with the bold ribbed banding became popular. The shape, the stamp patterns and the strap handles are part of a long provincial tradition. When thinly covered as here, it allows the light body to show through and produce overall a pale yellowish grey green covering. The soft frosty shine(very fine crystals formed on cooling) is one of the many variable characteristics of a high lime glaze.When thicker the glaze becomes greenish-grey and glassy - notice the runs near the base.
11101 Wide rim Yüe stoneware jar with 2 pairs of loops on the shoulders. From a Zhejiang kiln. Western Jin Dynasty 3rd to 4th C.AD H:31cm This graceful high-necked vessel has a bold, even dramatic, wide banded rim at the top. The contrasting curves from neck to the full rounded shoulders narrows towards the base, where there is a slight spread at the foot. The small double loops and the small but effective banding between body and neck are a foil to that striking, everted rim with the ribbed banding. Such an object shows the potter's skill and sensitivity to form and finish. The body has fired to a buff colour. The toasty colour in this case may be due to a little iron in the body or a slight amount of the glaze rubbed or wiped off. The pot was dipped upside down, neck first, in the glaze, submerged almost to the foot. The fired glaze surface has a soft smooth shine; the small oily runs, the dull greenish yellow crystaline finish are again typical. Of these three materials in the glaze, wood ash and clay can vary greatly from place to place. This simple recipe of two or three constituents mixed in varying proportions and fired on different bodies in different wood-fired climbing kilns, accounts for all of the variants seen in these pictures of south China pots.
11070 Yüe Ware Bowl on high foot 3rd-4tg c AD.H:8.5cm. Eastern Jin Dyn 317-420 AD. H:13cm BML Spur mark inside the bowl indicate that others were stacked above. Impressed rouletted bands of pattern were common on early Yüe ware Eastern Jin.
Red clay instead of grey clay in recipe These two examples brlow show the type of finish arrived at when a high proportion of iron is included in the basic recipe. The simplest method would be to replace some or all of the stoneware grey clay with red clay, though other rich iron materials could be used.
 LEFT 11077 and RIGHT 11105 Two similar black iron glazed chicken-head stoneware ewers. Southern Dyn 420-589AD. Each of these chicken-headed vessels with two square lugs on the shoulders is covered with a dark blackish-brown glaze by dipping. Probably from one of the Zhejiang kilns - possibly Deqing or Yuhang kilns, and dated around 360 AD. The colour of this ash/lime/clay glaze was achieved by additions of large amounts of iron oxide - using an iron rich mineral or by replacing much of the paler clay in the recipe with red clay. The slight differences of surface texture and colour are simply due to more or less iron and firing patterns.
 11085 and 11073 Two wide rimmed Jars Yüe ware 5-6th c.AD H:32cm BML The taller, narrower shape of these two jars compared with the rather squat form of the earlier examples is paralleled in the proportions of the chicken-headed ewers. On the right example, the grey-green glaze which covers most of the jar has a dull greyish tinge. This is said to have come from Yangzhou.
|
 |
|
|
|
 |
Yüeh 'Spirit Jars' large storage jars crowned with elaborate modelled lids
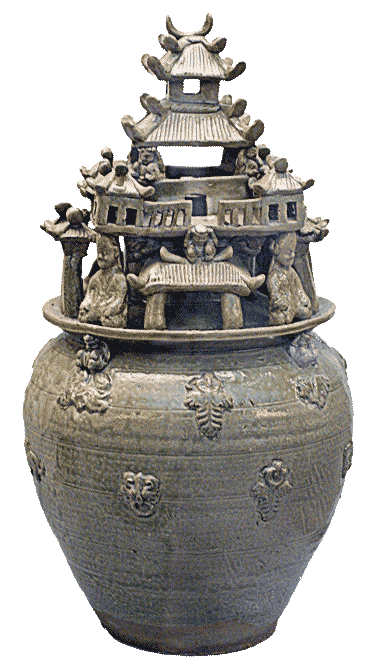 11069
One uniquely different type of Yüeh jar was the 'Spirit Jar', shen-t'ing, type of large storage jar crowned with an elaborate lid modelled in tiers with buildings and figures.
'Spirit Jars
 Green-glazed stoneware vases crowned with figures and buildings (proto-Yüeh ware. H:47cm Western Chin Dyn AD 265-316
The custom of portraying groups of immortals or Taoist deities took root in popular art in this district near modern Hankow. On bronze mirrors, made here in the 2nd century AD, appear portraits of the Queen Mother of the West and of the King Duke of the East with their winged servitors. The identity of the other spirits is less certain. About a century later a similar theme is taken up by the potter, but with differentiation of the immortals. The buildings on the vase are probably intended as their paradise in the western mountains.
11069 Spirit Jar (hun ping). late 3rd century.Yüeh ware Porcelaneous stoneware with olive green glaze.H:47 cm Large, extensively decorated burial jars like this have been recovered in recent decades. Limited to the area south of the Yangtze River in the Northern Chekiang and Southern Kiangsu province, they represent a vessel type and burial practices specific to this region. The lids, if we can call them that, seem sculptural pieces in their own right. They display an extremely rich assortment of buildings, figures, and animals. in a tiered architectural structure.
11069a Detail of lid.This detail shows the modelled quality more clearly. The jars were most likely placed in the tomb so the soul of the deceased would have a place to reside. This probably accounts for a palace-like structure of the lids with entrance gates facing the four directions. Most likely, the various figures represent Taoist immortals who somehow aided in the afterlife.
|
 |
 |
STAGE 6
The Jade Influence on Yüeh kiln production: Refined shapes and grey-green 'Celadon' type glazes
11071 Proto-Yüeh ware Lion-shaped Scholar's desk pot for ink or water. H.:17cm. Eastern Jin DynBy the 3rd and fourth centuries the Yüeh kilns in northern Zhejiang were producing stoneware with glazes which looked similar in appearance and hardness to jade. From lowly potters to scholars, civil servants and Princes, most would have recognised eventually the amazing similarities of some pieces of glazed Yüeh ware to the precious jade mineral. Some of the earliest Yüeh stoneware pieces Scholars "desk pieces", such as these two tiny glazed pots for ink and water, were clearly seeking to imitate similar valuable jade objects.
The "Jade Effect" raised the status of glazed stoneware pieces
11071 Proto-Yüeh ware Frog-shaped scholar's desk pot. Western Jin Dyn Soon the range of colours and textures of these glazed surfaces approached the superficial qualities of jade minerals. This extraordinary resemblance to a precious stone was in great part the reason for so many of these tiny desk objects being produced from the third century onwards.
Jade now had a profoundly stimulating effect on the production of such fine "green-grey-brown" glazed stoneware objects and resulted becoming fine art objects. Potters now strived to refine their bodies and glazes and firings, so that the results might satify a market which wanted jade-like ceramic pieces. The influence of jade continues throughout much of Chinese ceramics in various ways, as we shall see in later tutorials.
11074 Yüeh ware small lidded bowl, probably for cosmetics. 317-420AD Eastern Jin Dyn
The increasing number of examples of pale grey stoneware vessels with a celadon type glaze show the popularity and demand for paler more refined stoneware bodies with smooth stony surfaces and opaque greenish-grey glazes and shiny translucent/transparent grey green glazes on pale bodies. The greater variety of more elegant part-modelled forms is further evidence of the inflence of Jade and the prestige of this type of glazed stoneware.
|
 |
 |
STAGE 7
Other Important Influences on Ceramic Form 5th and 6th Century AD
In this uncertain world Taoism and Buddhism become increasingly popular
The wars, plagues, and political instability that characterize this lengthy period forced the Chinese to question traditional belief systems, especially Confucianism, and encouraged many to embrace Taoism and Buddhism, mystical religions each with beliefs of an Afterlife.
The influence of these two beliefs first begins to influence the shapes and decoration of ceremonial and funeral pottery in both the North and the South from the late Han period onward: Taoism with the stories of immortal deities, and Buddhism with the arrival of Buddhist pilgrims and priests with new mystical ideas and carrying small religious objects of precious stone, wood and metalwork in a fascinating alien style. All of this eventually feeds into Chinese ceramic forms, decoration and modelled imagery.
 LEFT 11086 Small flat dish on high foot with celadon glaze. Southern Dynasties 420-589 AD. RIGHT 11084 Small vase with celadon glaze Southern Dyn 420-580
Small votive objects associated with Buddhist ritual: a small pedestal dish and a vase, both made in the 5th Century AD, the forms copied from valuble metal vessels. The glassy fluidity of the glaze in the dish, and the heavy crackled glaze on the vase show a move towards glazes containing alkaline materials - increasing transparency, fluidity and crazing.
11102 Yüe brown-spotted, po-shan-lu incense burner with bird finial ca. 300 AD Late Western Jin Dyn H;11cm Yüe brown-spotted, po-shan-lu ("Magic Mountains") incense burner. The plain base section is a heavily potted deep saucer with an inner ridge, the incense container sits on a pedestal, the cover with three rings of four stylised petalled mountain peaks each hiding one circular aperture, the extreme top surmounted by a small bird. The whole cover is covered by a green-grey (celadon) glassy glaze of Yüe type with brown spots, the cover is also impressed with stars under the glaze. From a north Zhejiang Province kiln, possibly the Shanglinhu kiln.
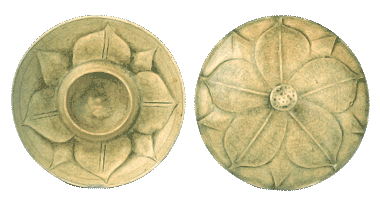
11103 Yüe covered dish with lotus pattern Southern Dyn. 6th C. AD H;8cm A Yüe covered dish,probably for cosmetics,the cover of which is press-moulded or/and carved in relief as lotus petals with a knob in the shape of a small lotus pod. The bottom section with a solid base is also carved in the shape of an open lotus flower with a shallow cup-like tray in the centre. The whole dish is covered with a thick,transparent glassy, crackled, yellowish-green glaze typical of the period and its southern provenance.
11075 Stoneware vase dull grey-green celedon glaze. Zhejiang Yüe Sui Dyn The wide rim, tapered neck, ovoid body, four coiled lugs; each element of this vase contibutes to this serene form - even the foil of the accidental glaze runs approaching the foot. The
11076 Jar witha cock's head, Zhejiang Province, Southern Dyn 6th C. AD Stoneware with celadon glaze. Compared with previous chicken-headed vessels, the shapes are changing and the components are beginning to flow into one continuous form. The handle grows out of the shoulder and the dragon's head dips into the wide rim. The chicken's head and the lugs on the sloping shoulders cluster closer to the rising neck.
The two parts of China; North and South, developing differently during the three hundred years of separation. In ceramics, the shapes of the vessels favoured in each region often differed considerably from each other. The North was especially influenced by immigration and influence from the north and West. This brought new forms and decorative ideas to ceramics. In the South many uniquely shaped vessels were developed in the many high-fire potteries of the South during the 3rd to 6th centuries AD. The differences would begin to blend together during the 6th century.
Northern Potteries in the 6th century
Foreign influences on design The sixth cemtury saw a lively trade growing up with the countries to the west. Sometimes the influence of the Sasanian Persians and the Central Asians is quite marked in ceramic form and decoratiion. Many foreigners had settled in the important cities. Ceramic activity begins to grow rapidly in the north during the mid 6th century AD. They began to emulate the stoneware of the southern Chekiang-Kiangsu region, producing tall vases with thick grey body and a glassy green or brown glaze, more fluid than the contemporary glaze of the south. C
11078 Info about pic here. 11078a Green-glazes stoneware jar with 'pie-crust' border. Northern Dynasties or Sui 6th C AD. Glazed stoneware similar to Yüeh ware were made in North-Chinese kilns towards the end of the Northern Dynasties period. Pots vary somewhat in body, glaze colour and composition and show different shapes. Characteristics are double-strapped loop handles, and the glaze often turns a bright milky blue where it is thick.
 11092 and 11093 Two stoneware jars covered with a yellowish-grey green glaze. Late 6th C. AD.H; ca.35cm This northern stoneware is paler, almost white when fired. More so than most southern examples. There are a great many large glazed jars witha double strip of clay looped into lugs and set vertically. In this one there are sprigged reliefs of rosettes and then a thin raised rouletted band. Below this decorative band is a broad area reaching to just below the the widest point It contains a simple but remarkably satisfying pattern of scratched vertical lines. A finally a raised band probably representing very stylised lotus petals. To an extent this acts as a glaze trap as the glaze ends here.
 11094 & Detail 11095 Wine vesseltsin with lotus pattern Southern Dyn Wuchang Hupeh.S & N Dyn 420-589 AD. Similar vases have been found in a tomb dated 565 AD. Probably from Jingxian Hebei province 6th C AD. Many Northern high-fired ceramics of this period have been found in Hebei province. This type of moulded and applied ornament is called "jewelled", though to have been made during the Northern Qi period(550-577) just before the reunification of China under the Sui. Such carving and ornament mostly on vases, include half-palmatte scrolls, beaded roundels and lotus petals. Most of the motifs are not Chinese, they reflect the great influence of Eastern Iranian and Buddhist metalwork patterns and forms, ultimately many Hellenistic designs which came to China with Buddhism often in the form of buddhist sculptures and small transportable ceramic or silver objects. By the sixth century Buddhism was well established in the North co-existing with Taoism and the teachings of Confucius.
Stoneware vase - wine vesseltsun with sprigged reliefs and grey-green glaze H:40cm Mid 6th C DA.Southern Dyn Wuchang The influence once again is Western Asian and Buddhist. But the quality and style is far below the previous example. Pale grey stoneware vase made in at least four thrown parts, decorated with thick rather grotesque applied mouldings of leaves. The four strap-like lugs, the coronet-like lid and the coarsely gadrooned bowl form rest on a high foot. It is an odd mixture of coarse decoration badly put together. It does however illustrate the existance of differences of standards of design and production. The glassy dull green celadon glaze is typical of such ceremonial vases of the North. There is a now an extensive range of pattern, ornament and styles about to be exploited.
|
 |
The Penguin Atlas of Ancient History: Colin McEvedy.
Patterns in Prehistory: R.J.Wenke O.U.P.
The Art of China Korea & Japan: P.Swain Thames & Hudson
The Search for Ancient China: C.Debaine-Francfort, Thames & Hudson
China, An Integrated Study: Cotterell & Morgan, Harrap Lomdon
The Chinese Potter: Margaret Medley.
Ceramic Art of China: Honey,Faber & Faber London
A Potter's Book: Bernard Leach,Faber & Faber London
KILNS Design, Construction and Operation: Daniel Rhodes, Sir Isaac Pitman and Sons, London
The Kiln Book: Frederick L. Olsen,Keramos Books, Bassett, California
|
 |
 |
This is the end of Ceramic History Tutorial 11
- and the third tutorial in
Ceramics in China 1 - 8.
 |
Sixth century China is about to be reunited. Potters are about to make another jump forward
both in earthenware and high-fire ceramics. Tutorial 12 will chart the ceramic developments in Classical Imperial China under the T'ang Rulers.
|
 |
In this next Tutorial
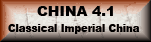
we explore the breadth and variety of
ceramic activity during the T'ang Empire
Adapted from the original versions which were written for my series of weekly illustrated lectures to ceramic students including those on the Harrow Studio Pottery Degree Course, Westminster University and The Central School of Art & Design, London UK from 1973 - 1994
Victor Bryant ©1994,2008
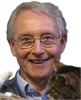
.
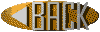
To Index Home Page
|
 |